As skillset change ‘Skilling Staff’ on war footing in textiles
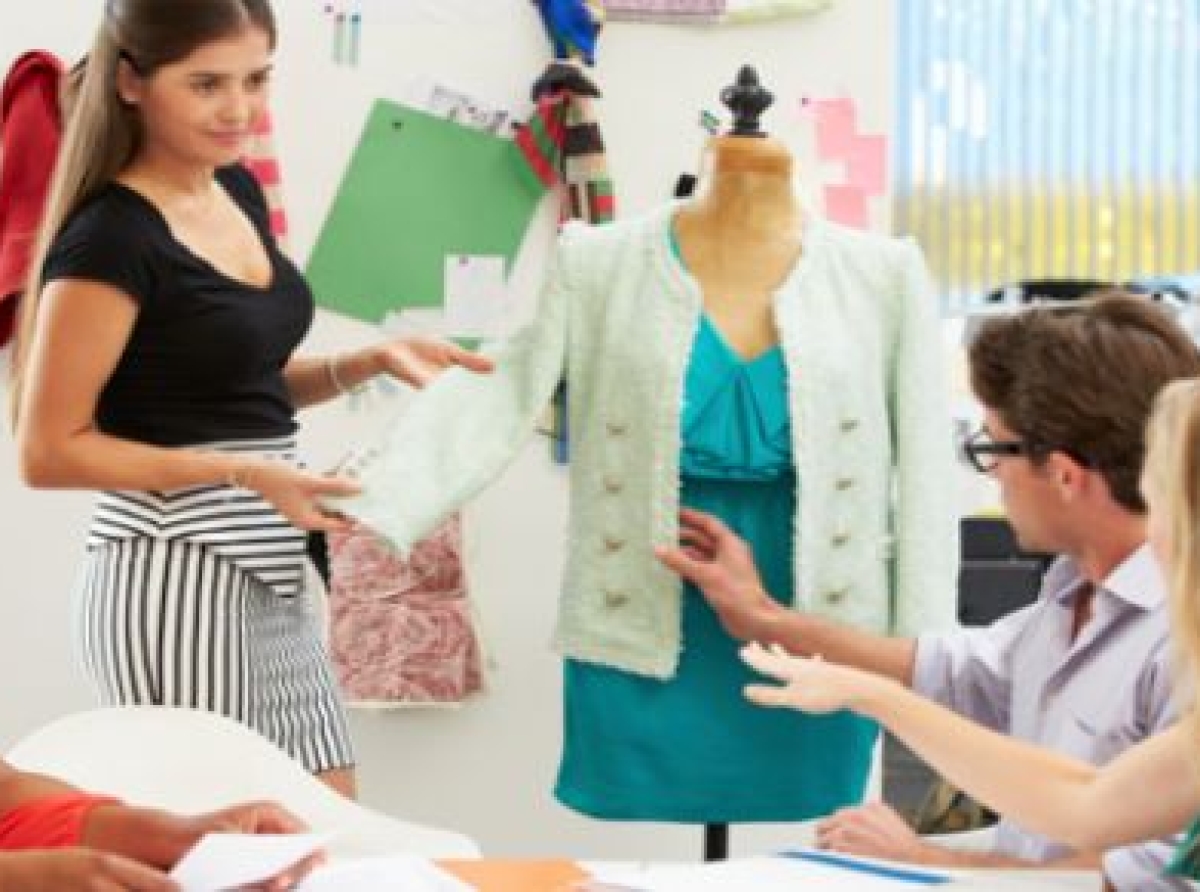
08 March 2023, Mumbai
Due to the labor-intensive nature of operations, garmenting accounts for significant employment in the textile industry. Fabric manufacturing job comprises the handloom, weaving, and knitting sectors. Later, we'll discuss how many people are employed across the value chain's operations.
According to estimates, around 50% of all handlooms, handicrafts, and sericulture workers are women. The household sector employs more women than registered small-scale or cottage units.
What will drive
Nearly every aspect of life has changed due to the global epidemic, including some developments for which we weren't necessarily prepared.
There is little doubt that the textile industry heavily relies to stay on course on nothing but skilled staff who as a pre-condition possess the requisite technical knowledge and domain expertise to run & operate complicated technical pieces of machinery enabling produce high-quality precision products/outcomes.
It is almost proven that investing in skilling staff can enhance efficiency multifold, raising the productivity bar, and the good thing is so is profitability, and it is in consonance with promoting innovation and helping attain enduring sustainability
There is a case for undertaking multiple measures:
-
Discoverability of skill gaps
-
Critical need for charting a training plan
-
Utilize existing resources available such as online training platforms
-
The need of the day is collaboration & greater alignment among educational institutions and industries
-
Recommended hands-on experience/on-the-job training
-
Making learning more interesting & engaging
-
Monitor and mapping as this whole exercise is work-in-progress Et al.
Change is the only constant
Dashboard; Against the backdrop of the rapidly evolving job market in the face of the new normal when emerging technologies are transitioning sector after sector, the paradigm is business imperative to stay invested in Reskilling, Upskilling & Newskilling (R.U.N) their workforce in Textiles.
Call to action (CTA) The urgent need for the textile industry is to adopt a "war footing" approach to skilling staff as their skillset changes prompting the immediate attention of the businesses.
Manufacturers might naturally get cracking by ramping up recruitment efforts to match the demands of this digital transformation along supply chains.
Gender equality
Let us take a legal view of Gender equality at a time when there is growing consciousness amongst the corporate world of looking at the bigger picture of meeting the goalpost of at last achieving it, as the caveat is besides this being a fundamental human right, today it is a business case given today, as it is an evidentiary finding in a medley of trade studies conducted in different parts of the world as an essential foundation for attaining a peaceful, prosperous and sustainable world as we move ahead.
Women gender in Indian society are posed with a range of challenges of different sorts & types while accessing, acquiring talent, and completing basic/quality education, training & building skillset, and more particularly while transitioning to attain respectably accepted/satisfactory employment in Indian society.
Nonetheless, the proportion of women employed in the organized sector must be improved, except in the clothing industry. Due to legislative constraints regarding labor rules and the financial benefits of small-scale units, the textile industry needs to be more cohesive.
As the textile units primarily participate in job activity, a sizable share of the workforce is employed in production-related activities. Moreover, there must be a clear distinction between the functions of sourcing, sales, etc., in the tiny units.
Advances in the sector
Technological advances would dramatically impact the profile of those participating. Just 2% to 3% of Indian textiles are made on looms without shuttles, compared to a global average of 16.9%, showing that the country's weaving sector is not very contemporary.
While the spinning industry in India is comparatively more advanced, just 1% of installed spindles are open-end (OE) rotors, and over 60% of installed spindles are older than ten years. India invests substantially less in special-purpose machines, which carry out specific tasks and enhance the product's value in the garment industry.
Relatively few export businesses have purchased cutting or finishing equipment. The sector would modernize due to the low level of technology and government incentives like TUFS. However, the high cost of power would be detrimental.
Technological advancement would result in the need for modern machinery training and increased internal training expenses. More automation will be prompted by labor scarcity and rising pay rates, increasing productivity. For instance, modernization has resulted in a drop in working hours per quintal of yarn from 77 to 25, and this trend will continue.
Also, due to automated cone winding machines, fewer workers are involved in post-spinning activities. The current technology would need experienced maintenance personnel with the necessary expertise. While pricey spare parts and machine downtime would substantially impact the industry's performance, proper maintenance would be essential.
Different strokes for different folks
Everyone has their own capability, aptitude choices, aims, and life goalposts and quite obviously preferences for the way they learn adopt/adapt to any chosen/default skillset in life.
There is a business case today that businesses must realize taking cognizance of considering talent as a strategic investment leading to a state of value-accretion, building efficiencies heft, quick adaptability to create natural resilience to not only weather challenging times responding rapidly/speed to market to the prevailing market conditions.
By now it is no more a well-kept secret that 'Skilling staff' is central to the sustainable growth of any textile industry success story resulting in a visible rise in the prospects of generating employment opportunities in a country like India anticipated to be the most populous country by 2023.
A more accommodating approach to labor laws will benefit the sector. The Contract Labour Act of 1970, which forbids contract labor for perpetual work, now governs the textile and clothing industries.
Aspiration of the sector; Our point is that sector consistently is looking up to the government of India to firm up the Labour Law Reform Strategy that, aims to improve making working conditions more conducive for all the stakeholders in the textile industry, which encompasses the key components such as fair wages and safe working environments making supply chains resilient and aligned to the reality of the day in an incredibly complex situation we find ourselves in.
Because of this, exporters need help to control the seasonal and order-based volatility in demand. More employment possibilities may become available if the rules are changed.
The laws as they stand also forbid women from working night shifts. Relaxing the same with sufficient safeguards might encourage more women's involvement and aid in addressing the industry's skills gap.
Latest Publications
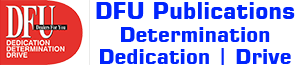