03 March 2023, Mumbai
Weaving refers to the process of interlacing yarn to produce textiles and fabrics In simplistic layman's terms/copybook style weaving per se can be well described as in effect,” A process of interlacing yarn to manufacture textiles and fabrics for that matter”.
Most intriguing is the timeless traditional weaving techniques (TWT) of textiles symbolic of the cultural heritage of societies globally. Interestingly these techniques, passed down through generations, mirror the unique artistic expression and historical perspective of each culture.
Historical perspective; Traditional weaving techniques in effect have been used for multiple centuries to create textiles that mankind has known. Broadly these techniques involve the interlacing of threads on a loom using varied patterns and processes, methods, emanating emphatically unique, intricate designs and textures.
Unravel
A quick context to the Traditional weaving techniques (TWT) is been that the use case of something ingrained in our proud textile lineage & practiced for the uncountable number of centuries sustainably creating the differentiated and proven ability to produce durable textiles.
Nitty-gritty; Often, woven fabric is more extended in one direction than the other. The warp refers to the threads that run lengthwise, while the weft refers to the other lines that join the warp and run widthwise. An end is a single, unbounded length of warp; a pick, or shot, is a single, unbounded length of weft that runs from one edge of the cloth to the other.
Typically, successive picks are lengths of a single weft thread that have been folded back on themselves several times. Before the size of the weft is introduced into the warp in all ways of weaving fabric, the warp is split into two sheets across a short length that extends from the already-formed cloth.
Shedding refers to both the operation and the shed, which is the area between the sheets. Picking is laying a pick of weft between the two warp sheets. The ends of each sheet are then moved partially or entirely to the location that was before occupied by the other sheet, forming a new shed with the required weave structure.
The weft is secured in place between two warp layers in this manner. Because it is impossible to lay the weft directly where the warp and already-woven fabric meet, a second procedure known as beating in or beating up is required to move the pick to the proper distance from the last one placed earlier.
Although pounding in often occurs as the shed transforms, it is typically finished before the new shed entirely takes shape. India has a varied and extensive textile history. Compared to other nations worldwide, it offered a large selection of textiles with various styles and made using multiple processes.
Quintessential Indian: Old techniques that can make a change
Each area develops a unique specialization in the weave of its textiles based on geographic location, climatic conditions, and cultural influences. Indian textiles are exquisite and well-suited to the country's environment. The textiles frequently have extremely detailed needlework on top of colorful weaves.
The Indus valley civilization is where Indian textiles got their start. The clothing of that civilization was woven from cotton that was spun at home. Household relics like bone needles and wooden spindles were discovered during excavations at Harappa and Mohenjodaro, indicating that humans spun cotton at home to create yarn and clothing.
In several locations, woven cotton fragments have also been discovered. There is a definite clarity around the Rigveda mentioning of weaving and containing the first written material on textiles in India. The Ramayana and the Mahabharata, two classic Hindu epics, reference many fashionable materials in the period.
India had extensive trading connections with other nations, and Indian textiles were well-liked in other ancient world nations. Throughout the first years of the Christian period, Rome was a favored destination for Indian silk. During the height of the silk route, cotton fabrics were also sent to China.
Throughout the 13th century, silk textiles from south India were sold to Indonesia. Even before the advent of the Europeans, India also sent printed cotton garments and chintz to Europe and Asian nations like China, Java, and the Philippines. Indian silk was traded for valuable goods from western countries in the 13th century.
The British East India Company dealt in Indian cotton and silk fabrics at the end of the 17th century, including the well-known Dacca muslin and sizable amounts of the same material created in Bihar and Orissa.
Reality check
The themes, patterns, designs, and weaving techniques still used by weavers today indicate previous textile and handloom traditions are still relevant.
Unquestionably traditional weaving techniques are holding out staying highly relevant even in the contemporary textile world as they enable achieve unique textures, vibrant patterns, and awesome cultural themes.
It is quite an open sector that TWTs in textile sector offers a rich vibrant heritage but unquestionably require a pulse check for usefulness in contemporary production processes.
Beyond any doubt, traditional weaving techniques of textiles have the most valuable contribution to promoting sustainable practices consideration and preserving time-old heritage crafts.
Epilogue
The most enduring value this rooted methodology called ‘Traditional Weaving Techniques’ imparts is that not only it has been in use for centuries together but, even today it continues to be an integral piece of textile production providing making textures unique limitless textures, alternatives to modern textile production & aesthetics let us just say which are otherwise hard to even replicate by machines of the day.
We have to underline & reckon here that, preserving and promoting these time-tested techniques is crucial for the cultural heritage and sustainable fashion of the country called India.
Latest Publications
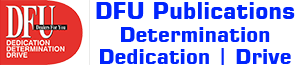