14 September 2022, Mumbai:
Due to its fragmentation and heterogeneity, the textile industry is one of the most complex industrial industries. It happens to be one of the top energy consumers, and without doubt in the textile mill, there is an upward tick in its electricity consumption. It is all owing to installation of modernized cutting edge machines and continuous usage of the advance & high output equipment replacing traditional tools & physical infrastucture.
Weaving uses about 23% of the energy, spinning uses 34%, chemical processing uses 38%, and other uses 5%. While electricity dominates the consumption pattern in spinning and weaving, thermal energy plays a significant role in chemical processing.
Two processes in textile mills use the majority of the thermal energy. They are water drying and water heating. The amount of water used in a textile mill directly relates to the amount of fuel utilized. So, cutting back on water consumption will also result in energy savings thus reduced water footprints.
Energy Management Quick Review
The fast development of process industries, which has resulted in significant energy consumption in textile operations, has made energy management been attached the utmost importance. And this has paved the way for energy conservation, which may be influenced by changes to processes and gear, the use of technological breakthroughs for process optimization, and the development of novel techniques to meet the challenge of significant energy savings in textile wet processing.
Therefore, replacing traditional procedures with more modern ones is necessary to save time, money, and energy significantly. Due to the global energy crisis and the high cost of fuels, increased efforts have been made to maximize energy conservation.
Energy is the new oil
One of the most important ingredients in every industrial operation is energy. However, the supply is not limitless. Due to the global energy crisis and the high cost of fuels, increased efforts have been made to maximize energy conservation. Energy Global economic crisis and rising fuel prices prompted an increase in efforts to save as much energy as possible. The fabric Industry is one of the sectors that use the most power and has the lowest energy utilization efficiency on record. Generally speaking, electricity is the primary energy used in the textile sector, equipment, lighting, cooling and temperature control systems, machinery, etc.
Whilst oil is fuel for boilers that produce steam, coal, and liquefied petroleum gas. And this has created a method for energy conservation that may be impacted by procedure, machinery adjustments, technology breakthroughs linked to process optimization, and new techniques to address the issue of significant energy savings in textile wet processing.
Energy saved is energy earned
The machinery used in the textile industry is often powered by electrical energy. The current oil, gas, and other fuel shortages have become essential cost drivers for every business.
Analyze electrical energy consumption and identify losses to increase energy conservation in the textile sector and ensure smooth operation. Any textile industry's processing unit is a crucial component where the completed product is produced. Because the processing area of a textile mill has a high energy usage share in terms of both the amounts of money and energy required, advanced energy conservation is thus crucial.
This article compares the effects of various machine operations, lighting load, electrical power losses, and energy conservation in the textile sector while saving 27614 kWh monthly, considering that it is one of the heaviest energy consuming sector & arguably has a dubious record of the least efficiency in energy utilization.
Join our community on Linkedin
Latest Publications
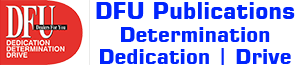