11 March 2022, Mumbai:
The Hon’ble Minister of State for Textiles and Railways, Smt. Darshana Vikram Jardosh inaugurated CITI’s Man-Made Fibre Conclave 2022 on 9th March 2022 held through a virtual platform.
The theme of the Conclave: US$ 450 Billion Global MMF Textiles Trade
Knowledge Partner – Wazir Advisors, Sponsors, Media Persons, and Delegates.
The Chief Guest
Smt. Darshana Vikram Jardosh, Hon’ble Minister of State for Textiles and Railways

ALSO READ: CITI’s Manmade Fibre Conclave'22: Virtual platform, 9th Mar
Smt. Darshana Vikram Jardosh inaugurated CITI’s MMF Conclave 2022, hailed the initiative of CITI for organizing such a timely and important Conclave for the MMF Sector being one of the thrust areas for this sector earmarked by the Government of India.
The Minister stressed that the Government is looking towards the inclusive and participative development of the Indian textile sector. and accordingly.
The Minister clearly alluded though it has its pain & pressure points and is fraught with the risk of getting directly pitted against better-prepared competition from the established players of MMF like China, Taiwan, South Korea, etc. clearly as they enjoy inherent advantages in terms of product quality, scale, lead times and prices.
The Hon’ble Minister exhorted the industry captains/ tycoons to look at investing in the MMF Sector and make best out of the schemes like PLI and PM MITRA supposed to be very supportive policies thus also provide huge employment opportunities for the Indian youths in this sector.
_large.jpg)
ALSO READ: Confederation of Indian Textile Industry’s (CITI), Hails Government’s Decision to set up Export Promotion Council for Technical Textiles
The Secretary (Textiles): Keynote Address
Again he also iterated that the growth in the textile sector can be achieved only through promoting right policies in the MMF Sector.
He was very categoric in his address nudging trade that," Globe is adopting China+1 policy for obvious reasons, and therefore, it is the right time for the Indian textile manufacturers to boost the trade of MMF products and reinforce our stature, position and above all our share in the global arena as India is certainly in sweet spot presently.
He said that the government is well seized of the present environment & precisely PLI and PM MITRA schemes were designed keeping in the mind the growth potential of the MMF sector.
He further emphasized and took pains to well apprise the industry that a number of states have shown interest to be a part of PM MITRA scheme for promoting the growth of the textile sector in their states and providing adequate employment opportunities. He alluded he is sanguine in his understanding about the trade," that good day are ahead".
Rajkumar congratulated the Hon’ble Union Minister of Textiles, Commerce & Industry, Consumer Affairs and Food & Public Distribution, Shri Piyush Goyal for successfully signing the India-UAE Comprehensive Economic Partnership Agreement (CEPA).
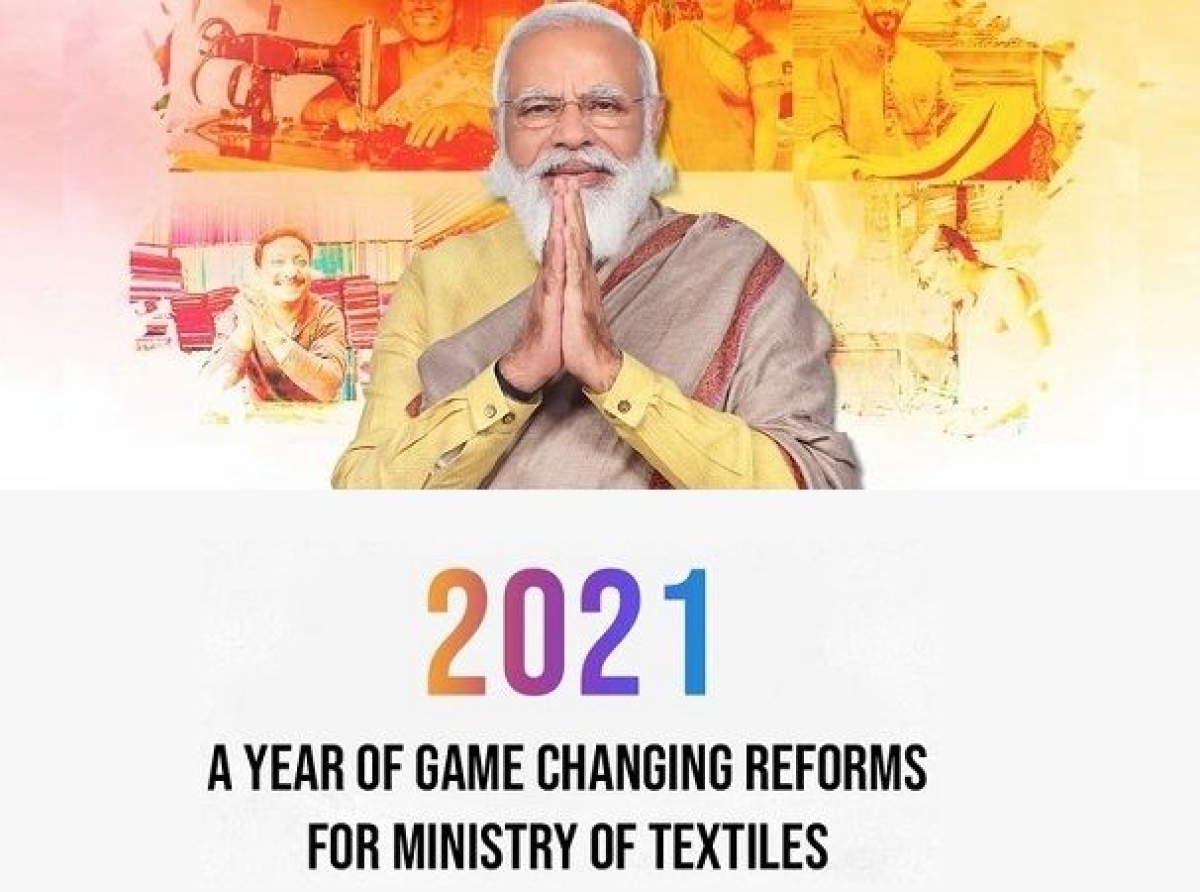
Welcome Address: T. Rajkumar, Chairman, CITI
Thanked profusely the Hon’ble Secretary (Textiles), Shri Upendra Prasad Singh, IAS, for taking out his precious time.
He expressed industry optimism about the ongoing trade agreements with the leading Textile & Apparel markets such as Australia, UK, EU, Canada, etc.
He categorically stressed that" The textile industry is very excited about this trade pact".
He very generously thanked the Hon’ble Minister of State for Textiles and Railways, Smt. Darshana Vikram Jardosh Ji, for inaugurating CITI’s MMF Conclave 2022.
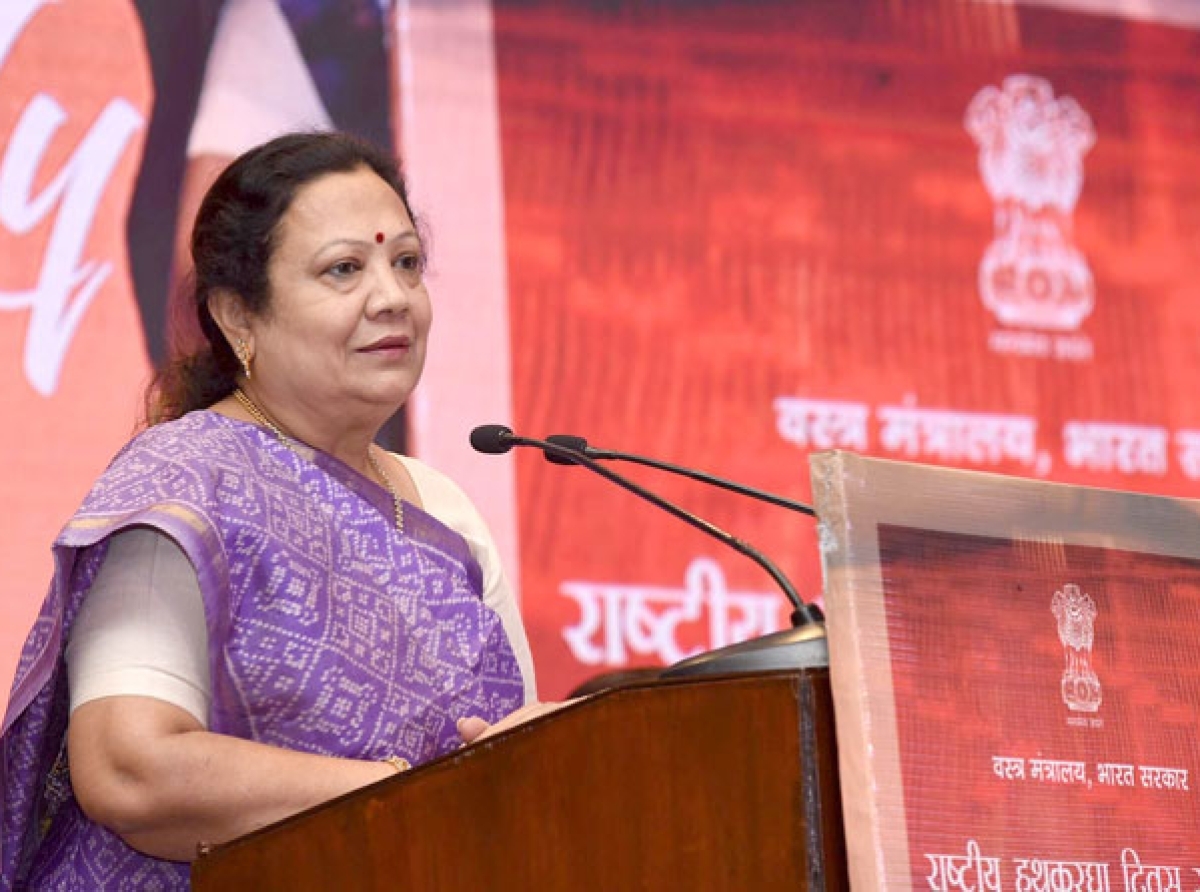
T. Rajkumar was very frank in pinpointing issues, such as
inverted duty structure
lack of technical know-how
huge dependence on imported machinery, etc. referring to them as bottlenecks in the all-around growth of the Indian MMF Sector.
He further appealed to the Hon’ble Minister that why not bring the entire MMF value chain under a 5% GST regimen thus solving long-term pain point/ industry-demand to address the issue of inverted duty structure (IDS)
The other issue he raised was to announce schemes for the production and development of MMF raw materials similar to that of natural fibres like cotton, wool, silk, jute, etc.
1st Session
Chaired by Shri O.P. Lohia, Chairman, Indorama Synthetic (I) Ltd.
2nd Session was chaired by Ms. Roop Rashi, Textile Commissioner at the Government of India.
Here, the Panelists held nuanced discussions on specific business opportunities for the Indian textile stakeholders in the context of changing global scenarios and Government thrust on the MMF Sector.
Vote of Thanks in the Inaugural Session
Rakesh Mehra, Deputy Chairman, CITI, and Chairman, Banswara Syntex Ltd. proposed this.
The eminent speakers and industry multi-stakeholders from both home & globally brainstormed/ deliberated the Sessions on “Global Market Situation and Emerging Trends in the MMF Based Textile Industry” and “Growth Opportunities for Indian Companies in the MMF Sector”.
_large.jpeg)
Vote of Thanks
R.K. Vij, Advisor, Indo Rama Synthetics (I) Ltd. proposed it on the successful completion of CITI’s MMF Conclave 2022.
The MMF Conclave 2022 was attended by over 500 plus delegates from all over the world and culminated in successfully sharing valuable trade insights.
RELATED ARTICLE (CITI) The Confederation of Indian Textile Industries: Textile industry seriously affected by high cotton prices
Join our community on Linkedin